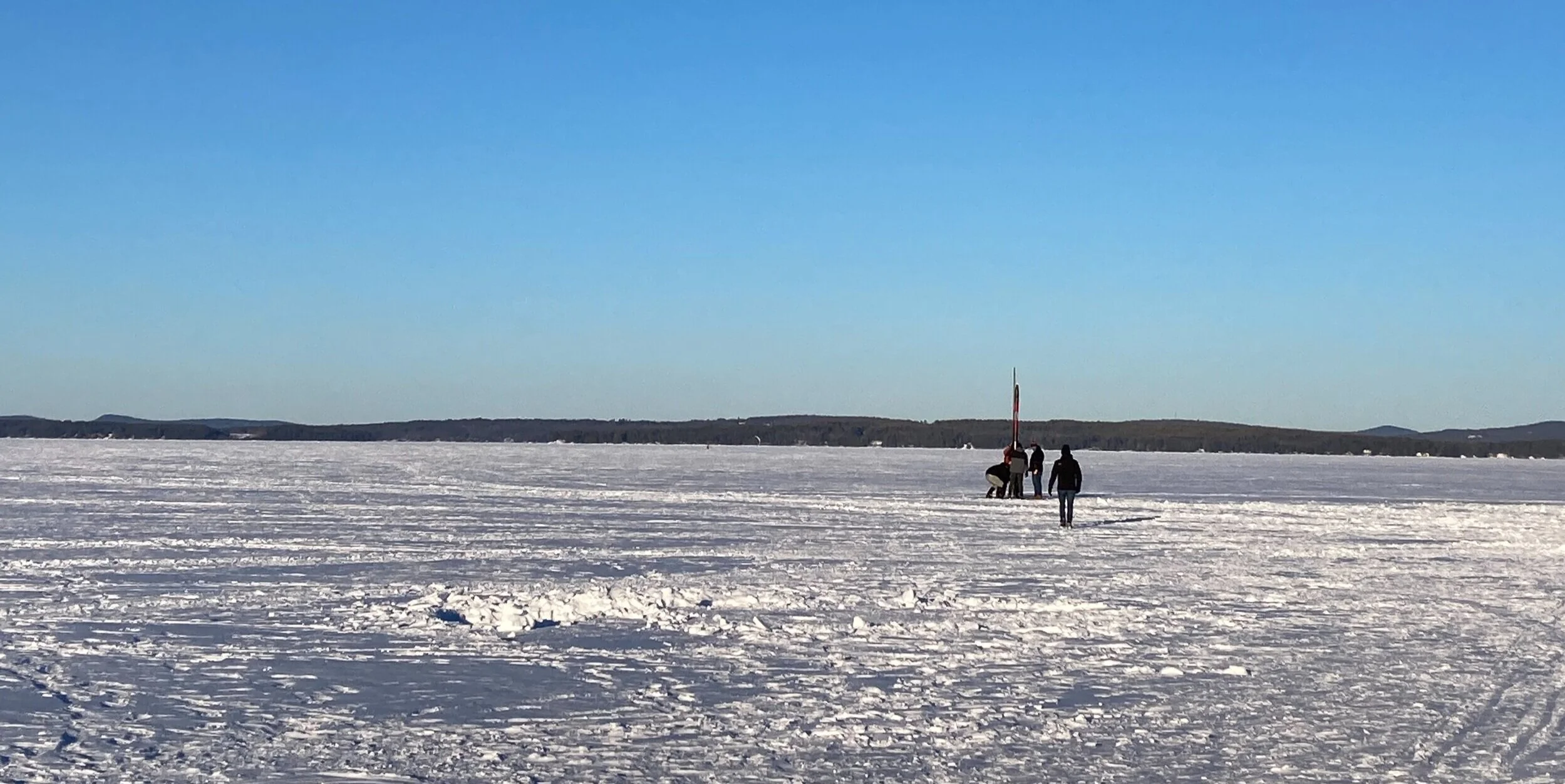
Northeastern University Launch Initiative (NULI) is a team under AeroNU that is competing in NASA’s USLI competition. We strive to teach new members all about rocketry while also engaging students of all ages in STEM activities. With 3 subgroups and a hardworking team of over 40 we believe we can meet all of the NASA requirements and deadlines.
Airframe
The airframe of a rocket is the structural skeleton, the outer protective skin that houses the motors, electronics, and payloads which incorporates subsystems from all teams.
This semester, the airframe subgroup will be working primarily on 2 rockets: Mark I and a custom two-stage rocket.
Mark I (pictured) is similar in form to the liquid vehicle, and will enable Redshift to test construction methods and systems beyond the scope of test bed rockets that the club has previously built. A successful launch of Mark 1 will lead to the development of MK2 which will also test the construction and ability to carry a liquid rocket engine.
To supplement the young and diverse team, the two-stage rocket was developed to allow newer members to understand the development & structure of a rocket while also challenging the experienced engineers within the club to build something unique! While it’s currently primarily in the design phase but will be built with custom electronics developed by the team, in addition to a fully modular and expandable airframe based on our lego-inspired 'paneling' concept. Currently, our custom boards have flown on consistent rockets to ensure their safety and responses, but we hope to implement, build, and launch a two-stage rocket by the end of 2023!
Avionics
Avionics refers to the electronics responsible for flight control and telemetry in a rocket.
Avionics works to develop custom sensing and control electronics and software for NULI. Currently we are developing the payload circuitry for the NASA USLI challenge, including a HAM radio transmitter. Another one of our main projects is our Flight Control Board, or FCB. These custom-designed printed circuit boards (PCBs) have a wide range of sensors including barometers, accelerometers, gyroscopes, and magnetometers which are all used for collecting data during Redshift rocket flights and deciding when parachutes or separation mechanisms should be deployed and controlled. FCBs also include radio and GPS that allows us to track rockets from the ground with a custom desktop application which shows flight data in real time.
To date, we have had over 20 successful FCB-controlled flights and continue to use them in more interesting and complex ways. Avionics is currently working on the fourth generation of this circuit board. We also continually add new features and improvements to the FCB and ground station software and are always working with other groups in AeroNU to provide rocketry electronics, such as the guided descent project.
Internal Mechanics
Internal mechanics handles the mechatronic systems and other moving parts within the airframe. They work closely with the Airframe subgroup to ensure the vehicles can support all the needed components.
In the past, Internal Mechanics developed several mechanisms for parachute disreefing, eventually settling on a nichrome-based line cutter. This allows Redshift to use a single large parachute rather than deploying a series of different sizes.
The team is currently working on our Marman clamp (pictured), which is a mechanical separation device that will take the place of black powder charges on our liquid-fuel rocket. Internal Mech is also developing a completely custom-designed separation device to fly on smaller rockets, as well as an 11-foot tall, 6-inch diameter solid-fuel rocket to use as a testbed for our projects.
Propulsion
Project Redshift’s liquid-propelled vehicle will fly on a regeneratively cooled bi-propellant engine, using kerosene and LOX. Propulsion designed, manufactured, and built the engine along with a test stand for data acquisition. The result is a 3D-printed Inconel engine consisting of regenerative channels, and a machined pintle injector. This engine has been cold-flowed and static-fired several times, with varying degrees of success.
This semester, the Propulsion team is designing systems to improve the reliability and robustness of the test stand and increase the chances for a successful firing. Other projects that are running concurrently with testing the engine include the design and manufacture of a vertical test stand for testing the flight stack up, a new augmented spark ignitor, and a swirl injector.
Prop-Software
Prop-software develops the control systems that allow the engine to operate optimally, along with other software for engine tests such as frontend data visualization, controls operation GUI, and data logging software. Our Engine Control Software is the centerpiece of the subgroup, following an inheritance-style design that allows verifying new features in simulation before deploying on the actual hardware.
This semester, the team is working closely with the Propulsion team to implement the proportional valve control in frontends and the engine control software to help prepare for a successful hotfire!
Meeting Time: Monday 8-10pm, Forsyth 244, 201, 241, MIE Capstone Lab
Wednesday 8-10pm, Forsyth 244, 201, 238, MIE Capstone Lab
Project Lead: Julia Rice, rice.juli@northeastern.edu